Beeindruckende Ergebnisse: Im Verbundprojekt GePart konnte gezeigt werden, dass der Leichtbauwerkstoff EPP im gesamten Werkstoffkreislauf einen deutlichen Beitrag zur Nachhaltigkeit erbringen kann.
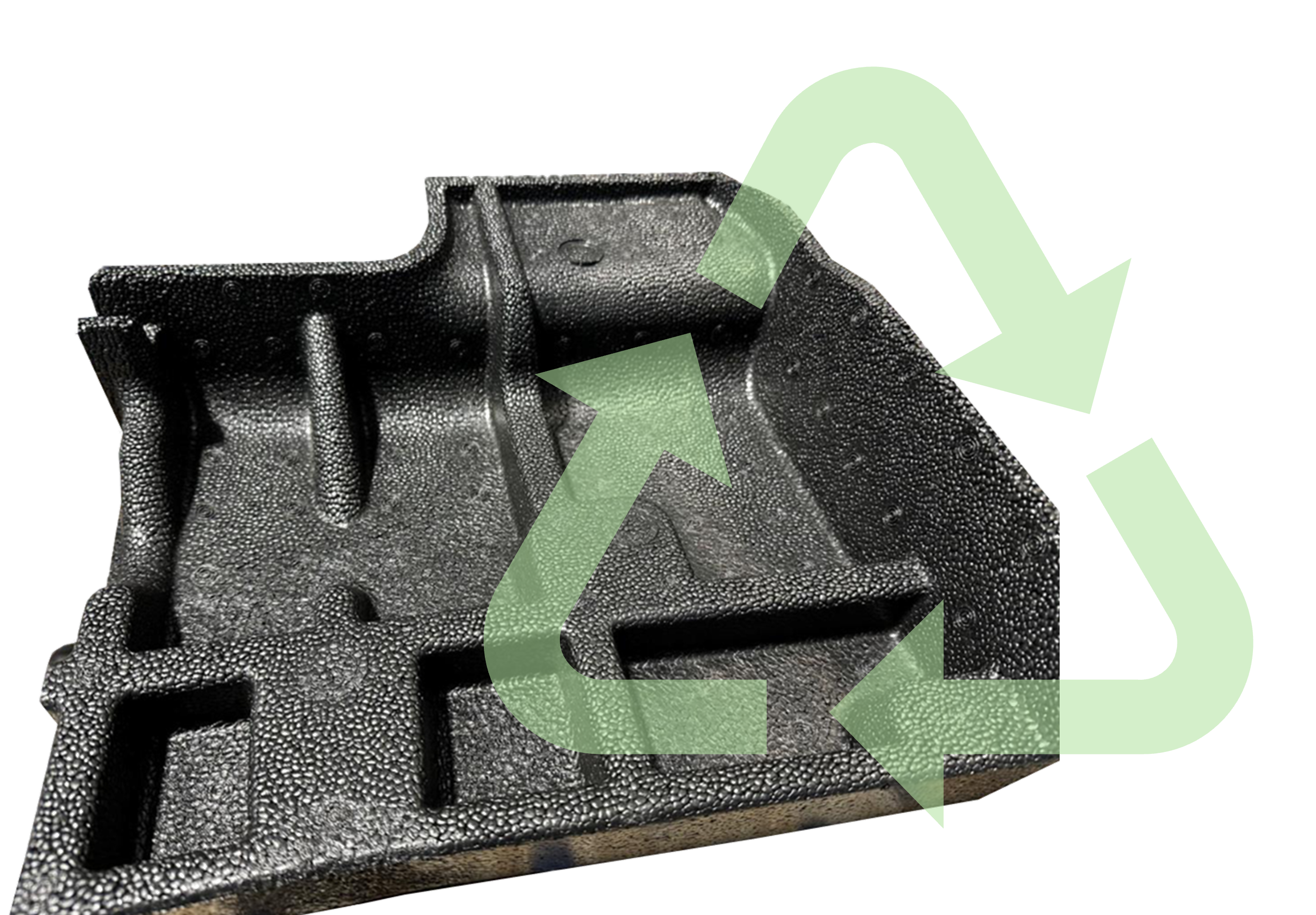
Expandiertes Polypropylen (EPP) ist in der Welt der Kunststoffe unter den Partikelschäumen ein echtes Multitalent. Der geringe Verbrauch an fossilen Rohstoffen bei der Herstellung dieses Leichtbauwerkstoffes aufgrund seiner geringen Dichte und hervorragenden Recyclingfähigkeit führt zu positiven Effekten im ökologischen Fußabdruck seines Werkstoffkreislaufs. Allerdings erweist sich der herkömmlich eingesetzte, vergleichsweise energieintensive dampfbasierte Formschäumprozess als deutlich nachteilig für die Ökobilanz.
Ziele des öffentlich geförderten Verbundprojektes „GePart – Entwicklung effizienter Verfahrenstechnologien innerhalb des geschlossenen Partikelschaum-Werkstoffkreislaufs“ waren es zum einen, diesen Kreislauf durch geeignete Recyclingstrategien und -verfahren zu schließen; zum anderen sollte eine energieeeffiziente Verarbeitungstechnologie entwickelt werden. Als Modellwerkstoff wurde EPP untersucht.
Für diese Arbeiten wurden die einzelnen Prozessschritte – vom Rohmaterial bis zum fertigen Formteil – sowohl für herkömmliches EPP als Referenzmaterial, als auch für das neu entwickelte rezyklatbasierte Rohmaterial r-EPP betrachtet. Dabei ermittelten die Partner Neue Materialien Bayreuth und Universität Dresden die Materialeigenschaften des r-EPP.
Die Ergebnisse des entwickelten r-EPP sind beeindruckend: Den Partnern Kaneka Belgium und R. Plast gelang es, den Rezyklatanteil im r-EPP auf deutlich über 70 % zu erhöhen. In Abhängigkeit des Rohstoffstroms waren sogar Rezyklatanteile bis über 95 % realisierbar. Neue Materialien Bayreuth und Universität Dresden ermittelten die Materialeigenschaften, die nur geringfügig unterhalb denen von EPP-Neuware lagen.
Als hinsichtlich der Energieeffizienz vielversprechender Verarbeitungsprozess stand die zum Zeitpunkt des Projektbeginns noch den ersten Anfängen befindliche radiofrequenzbasierten Formschäumtechnologie im Mittelpunkt. Die Anpassung dieses Verfahrens an das herkömmliche und das rezyklatbasierte EPP-Schaummaterial wurde von den Partnern Kurtz, T. Michel Formenbau und Neue Materialien Bayreuth vorgenommen. Um EPP mittels RF-Technologie verarbeiten zu können wurden polare Kopplungsmedien eingesetzt. Zusammen mit dem Partner Volkswagen entstand am Ende ein 3D-Demonstrator, der ein charakteristisches Formteil aus dem Automobilbereich abbildet. Die mechanischen Eigenschaften der Formteile aus RF-r-EPP liegen dabei leicht unterhalb denen von Bauteilen des dampfbasierten Referenzverfahrens. Weiterhin hat sich gezeigt, dass für eine weitere Optimierung der Oberflächenqualität zusätzliche Werkzeuganpassungen nötig sind.
Um die Umweltwirkungen der Herstellung des r-EPP und des RF-Verfahrens objektiv bewerten zu können, wurde eine projektbegleitende Ökobilanzierung (LCA) nach DIN EN ISO 14040/44 durchgeführt, für die der Konsortialführer des Projekts, Ruch Novaplast, die Verbrauchsdaten lieferte. Dabei konnte gezeigt werden, dass durch die Verwendung von Rezyklaten CO2-Einsparungen von rund 30 % im Vergleich zu Neuware möglich sind. Der Einsatz von dampfarmen bzw. dampflosen Verarbeitungstechnologien besitzt das Potenzial, die CO2-Emissionen des Formschäumprozesses sogar um bis zu 35 % zu reduzieren.
Das Projektkonsortium umfasste die Forschungseinrichtung Neue Materialien Bayreuth GmbH, R. Plast GmbH, Ruch Novaplast GmbH, Technische Universität Dresden, T. Michel Formenbau GmbH & Co. KG, Volkswagen AG, Kurtz GmbH sowie Kaneka Belgium NV als assoziierten Partner. Das Verbundprojekt wurde durch das Bundesministerium für Wirtschaft und Klimaschutz (BMWK) im Rahmen des Programms „Technologie-Transfer Programms Leichtbau“ unter dem Förderkennzeichen 03LB200F gefördert. Die Begleitung des Projektes erfolgte durch den Projektträger Jülich.
Ansprechpartner
Neue Materialien Bayreuth GmbH
M. Sc. Thomas Frank | E-Mail thomas.frank@nmbgmbh.de