Eine neu entwickelte Verfahrensvariante des Laserauftragsschweißens ermöglicht die Senkung der Bauteilkosten. Auf der Prototypanlage im Technikum der Neue Materialien Bayreuth GmbH können hierzu Versuche und Entwicklungsarbeiten durchgeführt werden.
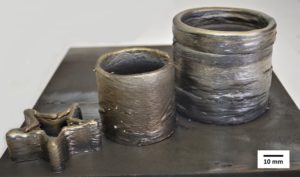
Das drahtbasierte Laserauftragsschweißen bietet eine wirtschaftliche Verfahrensalternative zur pulveradditiven Fertigung, da hier kostengünstigere Metalldrähte für den Schichtaufbau verwendet werden. Die Neue Materialien Bayreuth GmbH beschäftigte sich zusammen mit Partnern im Rahmen eines öffentlich geförderten Projekts mit der Weiterentwicklung dieses Verfahrens. Ziel war es, die Herstellungskosten zu senken und dies zudem bei erhöhten Auftragsraten.
Die Lösung liegt darin, den drahtförmigen Ausgangswerkstoff vor dessen laserinduziertem Aufschmelzen zu erwärmen. Durch eine solche Vorerwärmung können die für das Aufschmelzen des Drahts erforderliche Laserleistung und damit die Bauteilkosten reduziert werden. Dies gilt auch für den spezifischen Energiebedarf bei Einsatz dickerer Drähte, durch den höhere Aufbauraten erreicht werden können.
Die Neue Materialien Bayreuth GmbH verfügt in ihrem Technikum über eine Prototypanlage für diese innovative Verfahrenslösung. Gegenüber herkömmlichen Anlagen ist sie mit einer Drahterwärmungseinrichtung ausgerüstet, mit der die oben beschriebenen Prozessverbesserungen umgesetzt werden können. Weiterhin ermöglicht eine Infrarot/Optische-Kamera die insitu-Überwachung des Schmelzbades, so dass der Aufschmelzprozess optimal eingestellt werden kann. Damit kann aufgrund geringer Eigenspannungen und homogener Eigenschaften eine verbesserte Bauteilqualität realisiert werden.
Die Anlage besitzt einen Bauraum von 400 x 400 x 500 mm und erzielt Bauraten von 100-200 cm³/h. Verarbeitet werden können Stähle, Superliegerungen, Refraktärmetalle. Zur Verarbeitung von reaktiven Materialien, wie Titan, kann der Schichtaufbau nach Hochvakuumierung (≤ 5×10-5 mbar) unter Schutzgas durchgeführt werden.
Auf der Anlage können komplexe Bauteile, hybride Bauteile aus verschiedenen Werkstoffen sowie Bauteile, die mittels additiver und subtraktiver Fertigung hergestellt wurden, aufgebaut werden. Möglich ist auch eine Kombination aus verschiedenen additiven Verfahren.
Das Verfahren sowie der entsprechende Anlagenprototyp wurden im Rahmen des vom Bundeswirtschaftsministerium geförderten Projekts „AdLeS – Verfahren und Anlagenprototyp zur additiven Serienfertigung von großen und komplexen Leichtbaustrukturen aus hochfesten Legierungen“ (Förderkennzeichen ZF4064604) von den Kooperationspartnern Neue Materialien Bayreuth GmbH Evobeam GmbH, Ircam GmbH und ISEMP entwickelt.
Ansprechpartner
Neue Materialien Bayreuth GmbH
M. Sc. Agata Kulig | E-Mail agata.kulig@nmbgmbh.de